この記事ではQCの7つ道具管理図について、説明します!
![]() パレート図 | ![]() 特性要因図 | ![]() グラフ | ![]() チェックシート | ![]() ヒストグラム | ![]() 散布図 | ![]() 管理図 | |
---|---|---|---|---|---|---|---|
主な用途 | 複数の問題から、重要な問題を絞り込む | 問題の因果関係 整理 | データの図示化 | データの層別 手順漏れ防止 | ばらつきの把握 | 1組のデータの 関係性/相関の整理 | 工程の コントロール |
問題点把握 | |||||||
原因分析 | |||||||
効果確認 |
管理図とは?
品質管理をやるのであれば、必ず知っておく必要のある管理図。これは、製造工程が安定しているのか否かを統計的に、簡単に判断できるツールになります。
人の感覚や経験値でなく、データとして工程を管理していく際に管理図を用いることで、客観的に判断できるようになります。
工程が管理された状態とは?
そもそも工程が安定した状態、管理された状態とは、どのような状態を指すのでしょうか?
これは、ズバリ製造した製品にばらつきが無い(少ない)状態が工程が安定しているということができます!
とはいえ、モノを作る以上ばらつきは発生します。
ただし、基本的にばらつきには2種類(良いばらつきと悪いばらつき)あることを前提として認識してください。
ばらつきの種類
- 1. 偶然発生するばらつき (偶然原因によるばらつき)=管理されたばらつき
-
作業標準通りに製造していても、発生してしまうばらつき。
これは、同じ材料やマシン/人で製造しても、少しずつばらつきがあるために発生してしまうもの。
データをプロットすると、正規分布を取ります。 - 2. 工程異常によるばらつき(異常原因によるばらつき)=管理されていないばらつき
-
作業ミス、異種材料混入や加工機の摩耗など、作業標準外の事象が原因で発生するばらつき。
これが存在する工程は、安定していない工程と考えます。
では、ここで問題です。直感的に捉えて、下記のどちらの図(A / B)が管理されている状態と思いますか??
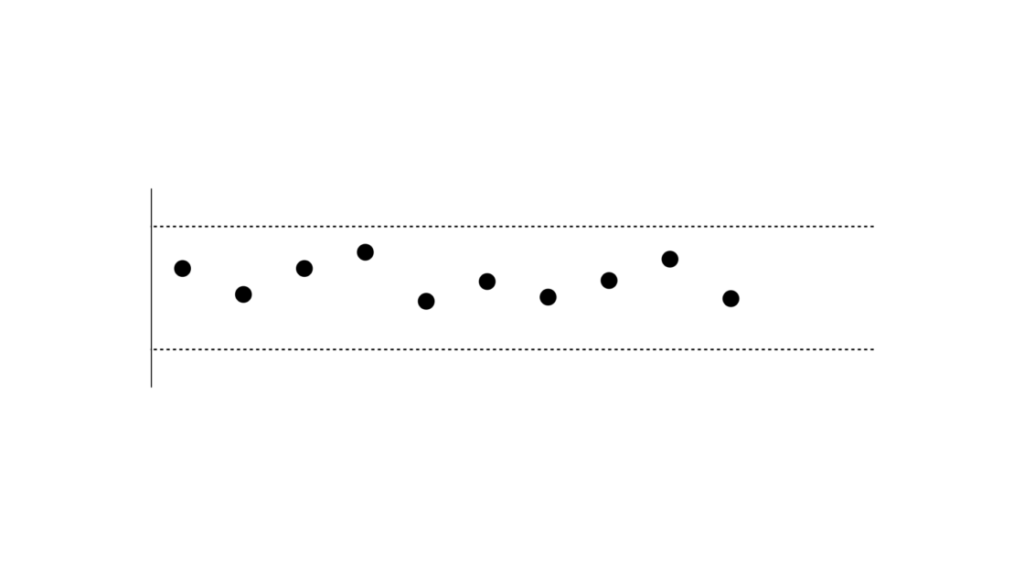
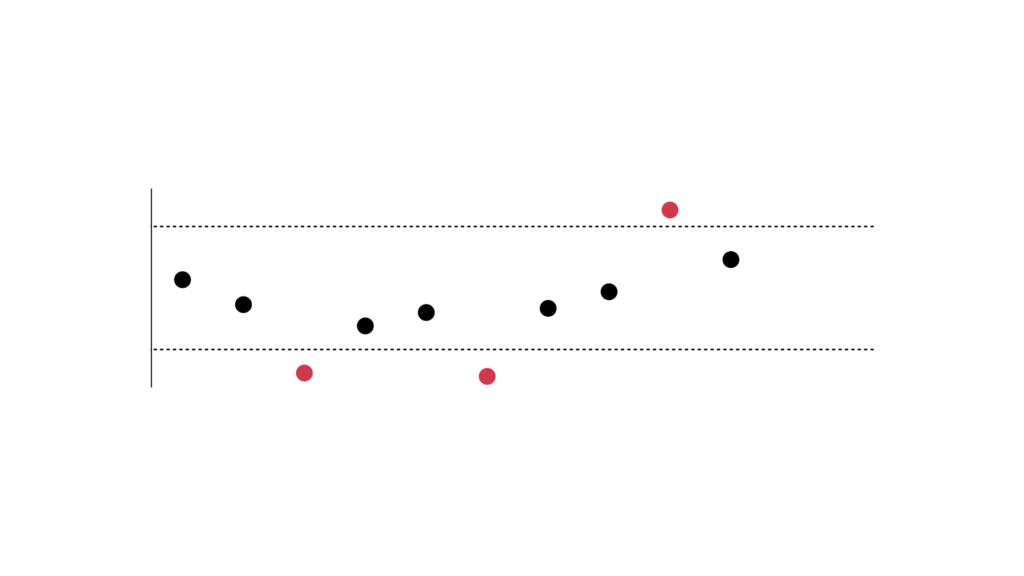
正解はここをクリック(タップ)!
Aです!
なんとなーくわかるかな?と思いますが、まさにここに示した図が管理図で、ドット(例えば寸法平均値)が上下の点線を超えるとNG (管理限界線を超える)となります。
製造工程内の製品の管理したい値のばらつきを見て、プロットし、異常なトレンドを示した際には、工程が安定していない状態と判断することができる、そんなツールが管理図になります。
管理図の仕組み
先ほど説明した通り、管理図とは統計的に求めた上下の限界線を持つ図になります。
では、下記の上下点線(管理限界線)はどのように統計的に定めているのでしょうか??
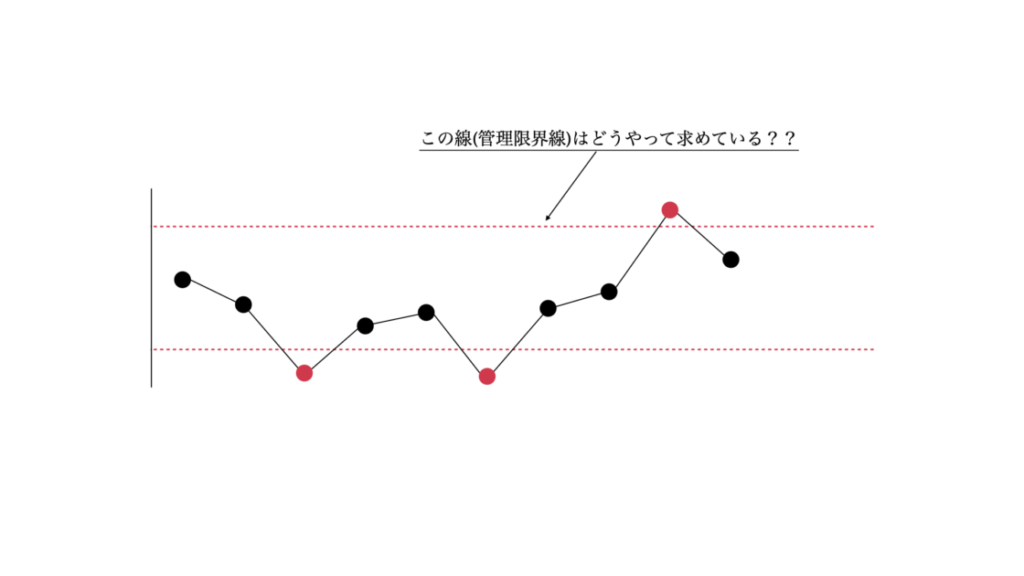
この赤線は一般的に±3σ(スリーシグマ)にて設定されています。
シグマσとは??
シグマって何??という方に簡単に説明すると、σ=標準偏差と呼ばれるデータのばらつきの指標になります!
複数のデータがあったとき、そのデータのばらつきを表現するのにσ(標準偏差)を使って表すことができます。
データを取得/加工し、平均値をとった際に得られる分布は正規分布になるので、これをσ(標準偏差)別に分けていくと下記図のようになります。*正規分布曲線作り方の参考サイト
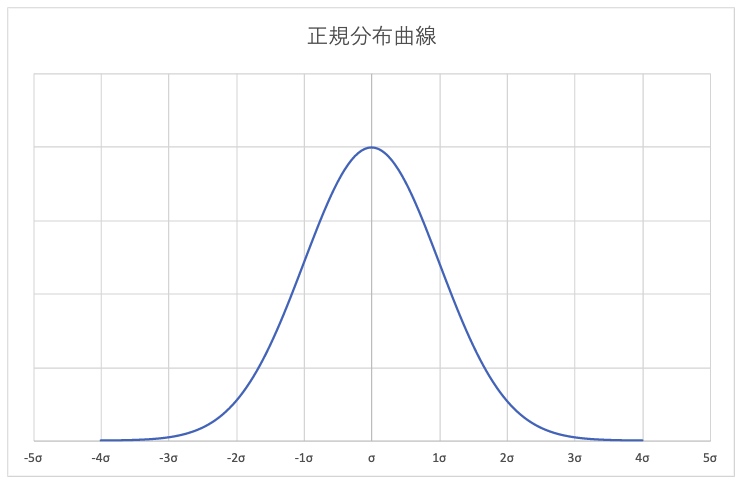
これだけ見ても何のこっちゃ?かもしれませんが、シグマ別(標準偏差別)正規分布と確率を下記に記載します。
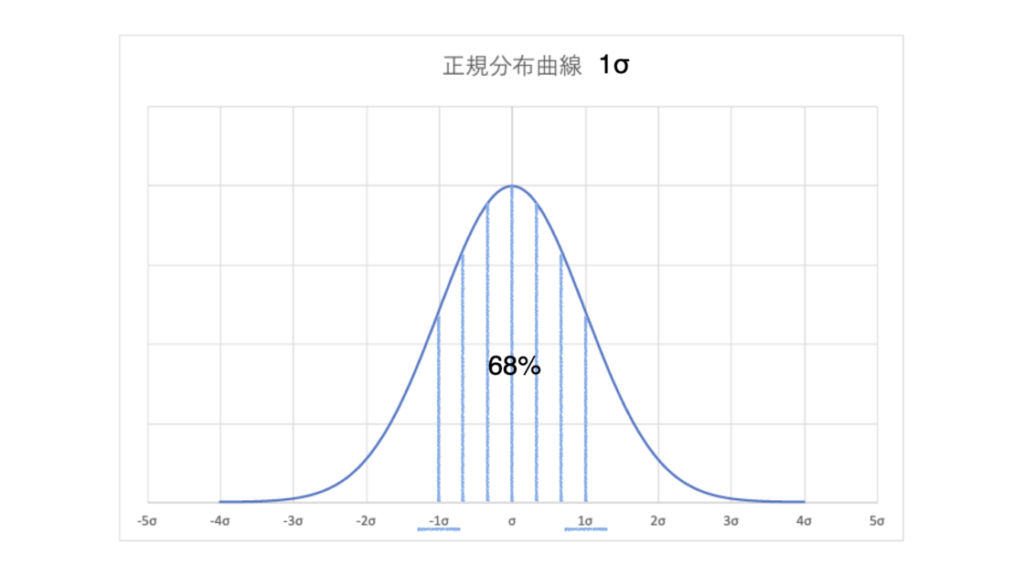
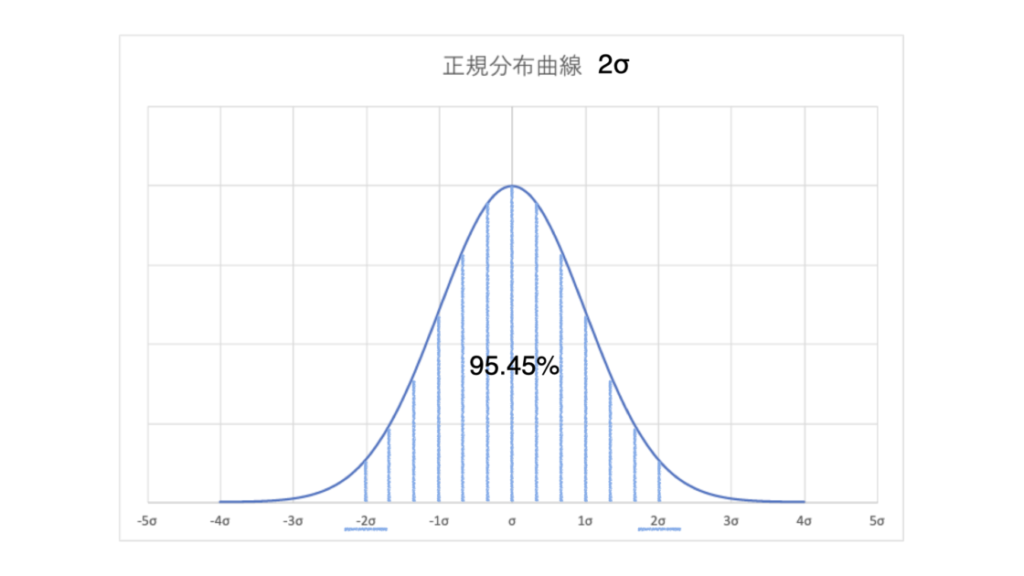
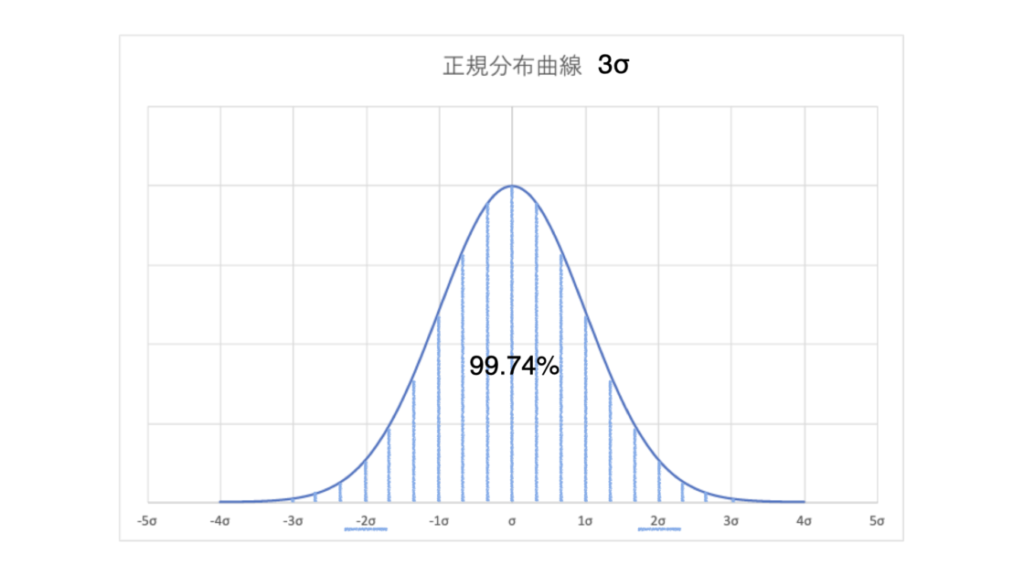
この正規分布の確率を見て、ピンと来た方も多いと思います!
先ほどの管理図にて±3σにて限界線を引くと記載しましたが、この確率がポイントです。
測定されたデータ/管理したいデータは基本的に正規分布を取るため、±3σを管理限界にすることで、99.74%は限界線内に入るというロジックになります。
よって、1000コのデータがあれば、997コは管理限界線内に入るということです。
管理限界線をサンプリングをして取得したデータの平均値は基本的に線の内側にある、ここから外れるデータは異常ということがよくわかると思います。統計的には1000コ中3コ外れる。
ちなみに各シグマレベル別に確率を記載すると下記の通りです。
σレベル | データが入る確率(%) | データが外れる確率(%) |
---|---|---|
±1σ | 68.3 | 31.7 |
±2σ | 95.45 | 4.55 |
±3σ | 99.74 | 0.26 |
±4σ | 99.9937 | 0.0063 |
±5σ | 99.999943 | 0.000057 |
±6σ | 99.9999998 | 0.0000002 |
管理図の種類
今までの説明で、管理図は工程が管理状態にあるか/安定した状態になっているか、をデータを元に判断することのできるツールであることを理解できたと思います。
また、データの範囲については3σ(99%)の管理限界線を元に管理しており、ここを外れれば異常/安定していない/ばらつきのある工程であることも理解できたかな、と思います。
この管理図には下記のように複数種類があり、ここでは代表的なXbar-R管理図を紹介します。
- Xbar – R管理図 :計量値の平均値の変化とばらつきの変化を見る
- Xbar – s管理図
- X – R管理図
- p管理図
- np管理図
- c管理図
- u管理図
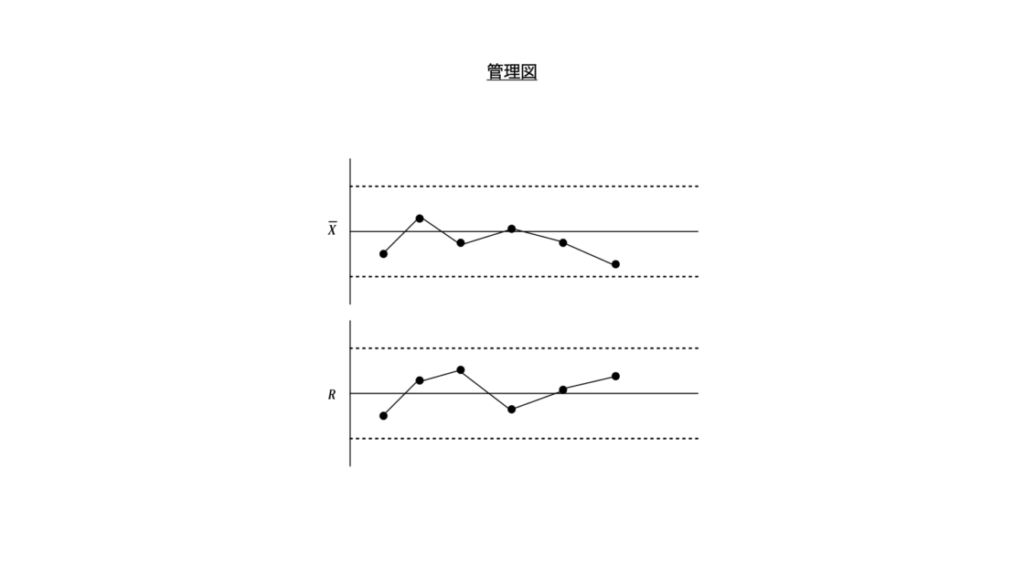
Xbarはデータのまとまり(群)の平均、Rは群の中の最大値-最小値にて求めます。
また、上記で点線で示している管理限界線(UCL:上方管理限界 / LCL:下方管理限界)は求められた±3σを元に引きます。
(ちなみに3σの近似係数として、管理図のための係数表があり、それを使うのが主になっています。結果もほぼ変わりません。)
おそらく、どこの企業もシステムにて管理図を自動的に作れるようにSPC管理システムが存在していると思いますが、作成ロジックは理解しておいた方が良いですね。
管理図の見方
当然管理図は書いただけでは役に立たないので、管理図を元に情報を読み取る方法を身につける必要があります。
管理図の見方の原則として、下記があります。
- 管理図の点は、個別でなく分布として見ること。母集団の分布がどうなっているかを考える。
- どうしてもばらつき(偶然ばらつき)は生じるので、点の動き自体に執着しないこと。
- 基本的に限界線内に入っていれば、工程は管理状態とみなすこと。
ではどのような状態が管理されていない/安定していない管理図なのか、数例を紹介します。
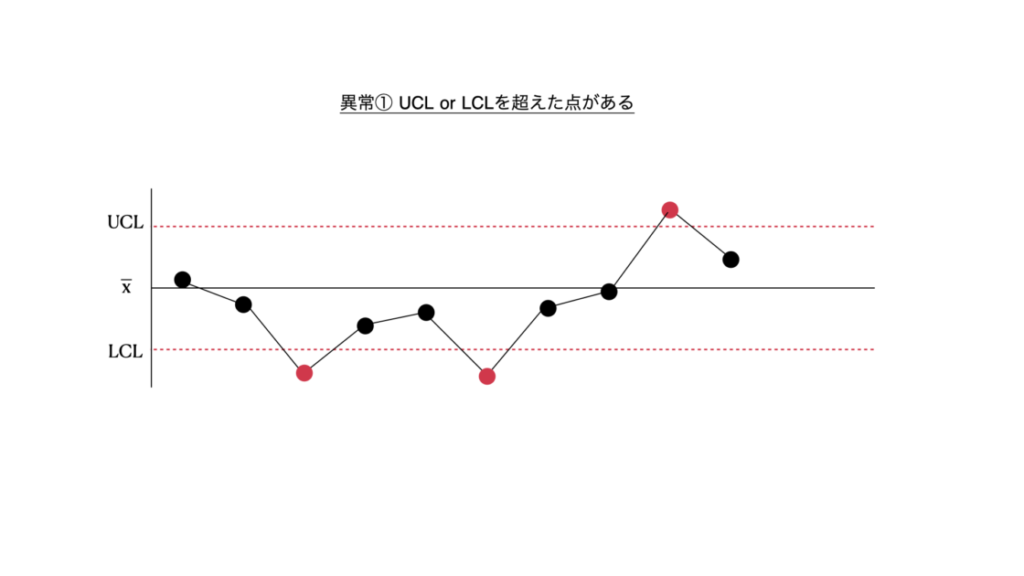
異常① UCL or LCLを超えた点がある
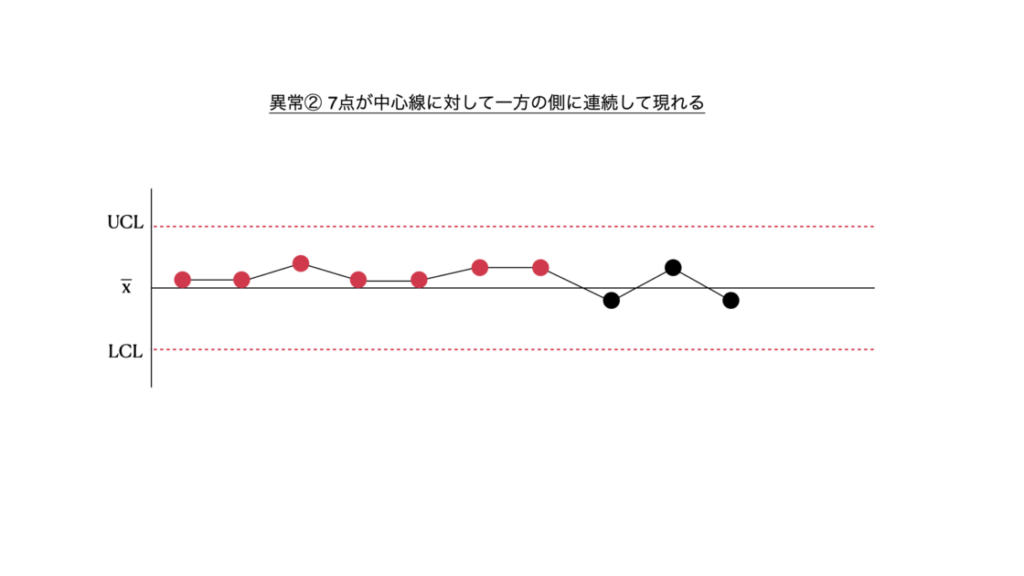
異常② 7点が中心線に対して一方の側に連続して現れる
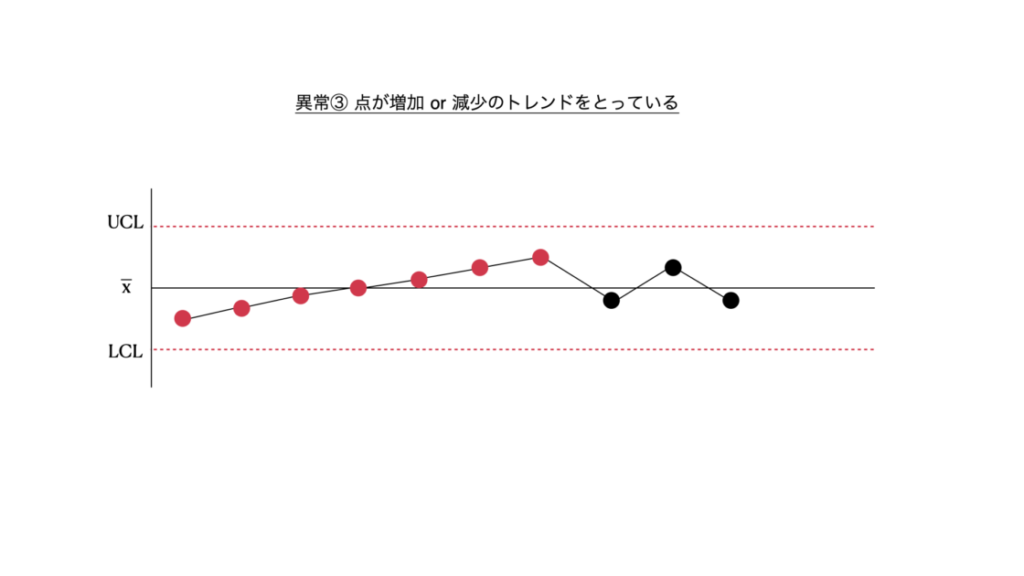
異常③ 点が増加 or 減少のトレンドをとっている
このようなトレンドが見られた場合、何か工程で異常が起きている!と、すぐに判断できるようになっておきたいですね!
まとめ✔︎
統計的な考え方を使い、工程の安定状態が直感的に誰でも理解できる管理図。
どのような仕組み/思想で作られているか、をしっかりと理解した上で使っていきたいですね!
今回はこの辺で終了といたします!ありがとうございました!